La tecnología le abre las puertas a operaciones más seguras, a menores costos y con mayores controles. Ventajas de una solución que suma adeptos.
Las unidades con Autopilot tienen una diferencia fundamental: saben todo lo que deben hacer.
En estado de explosión es el momento que atraviesa la automatización a nivel global. Desde vehículos hasta equipos para movimiento de materiales, como transpaletas, apiladores y contrabalanceados, están siendo transformados con las nuevas tecnologías que pueden prescindir de operarios para su conducción.
Poco a poco, los depósitos cerrados comienzan a colocar sistemas en el que los equipos se manejan de forma autónoma. Estos proyectos están transformando las formas de trabajo, optimizando tiempos, costos, evitando accidentes y, por lo tanto, haciendo más competitiva a cualquier empresa logística que busque ganar terreno en el mercado.
Para explicar las ventajas de la automatización, Stefan Blom, LogisticsSolutions Manager, y Måns Pontén, Application Manager, ambos de Toyota Material Handling International, estuvieron de visita en la Argentina. Durante su estadía, los directivos suecos evaluaron proyectos a futuro en los clientes locales de la marca.
Las unidades con Autopilot tienen una diferencia fundamental: saben todo lo que deben hacer. Por ejemplo, el recorrido conveniente entre diferentes puntos. “Generalmente las unidades están conectadas con el WMS, que es el sistema que administra los depósitos. Así se optimizan los recursos y se evita pérdida de tiempos, al elegir el sistema las rutas más eficientes”, afirmó Blom.
Este tipo de unidades “no necesitan ir al baño, ni al dentista, ni nada”, graficó el especialista. No tienen descanso y son de uso intensivo. “Hay mucho desgaste de los equipos al mando de personas. En cambio, con el sistema automatizado los movimientos son menos bruscos. Se ahorra en mantenimientos, al no haber tanto desgaste en materiales, como ruedas y demás componentes”, explicó Pontén.
Además, comentó que los equipos cuentan con la opción de dirigirse al lugar indicado para recargar energía de forma automática. Por lo pronto, es menos costosa una operación autónoma que manual.
.
Sin riesgos
Los especialistas suecos explicaron, durante una entrevista realizada en las instalaciones de Toyota Material Handling, en la localidad bonaerense de Don Torcuato, que los equipos con Autopilot no ocasionan ningún daño a la propiedad ni a los productos.
“Poseen un scanner para controlar lo que ocurre a su alrededor y evitar accidentes con personas y objetos. Al tener cámaras, son cien por cien seguros. Según la zona, disminuye o no la velocidad y enciende luces para prevenir y alertar a operadores que puedan encontrarse en lugares inadecuados. No hay riesgo para los seres humanos”, coincidieron Blom y Pontén.
Por otra parte, el mantenimiento mecánico es el mismo que tiene un equipo común, aunque tiene un desgaste mucho menor.
Los equipos, además, cuentan con el sistema de gestión de flotas I_Site – existen 100 mil unidades ya conectadas en el mundo-, que da información en tiempo real sobre todo lo que ocurre con los equipos en funcionamiento. En principio, un operario para manejarlo tiene que introducir un código de acceso personal. A partir de ese momento, el sistema bridará diferentes datos, como la tasa de utilización del equipo asociado al conductor correspondiente, registro de los impactos, historial de carga de la batería, entre otros.
La compañía brinda el servicio de posventa para acompañar al cliente ante cualquier inconveniente o ante un eventual desperfecto mecánico. Desde el área de Automatización, la marca puede intervenir en forma remota cualquier unidad Toyota automatizada, a través de una conexión VPN segura a la red de Autopilot.
Los especialistas suecos explicaron, durante una entrevista realizada en las instalaciones de Toyota Material Handling, en la localidad bonaerense de Don Torcuato, que los equipos con Autopilot no ocasionan ningún daño a la propiedad ni a los productos.
“Poseen un scanner para controlar lo que ocurre a su alrededor y evitar accidentes con personas y objetos. Al tener cámaras, son cien por cien seguros. Según la zona, disminuye o no la velocidad y enciende luces para prevenir y alertar a operadores que puedan encontrarse en lugares inadecuados. No hay riesgo para los seres humanos”, coincidieron Blom y Pontén.
Por otra parte, el mantenimiento mecánico es el mismo que tiene un equipo común, aunque tiene un desgaste mucho menor.
Los equipos, además, cuentan con el sistema de gestión de flotas I_Site – existen 100 mil unidades ya conectadas en el mundo-, que da información en tiempo real sobre todo lo que ocurre con los equipos en funcionamiento. En principio, un operario para manejarlo tiene que introducir un código de acceso personal. A partir de ese momento, el sistema bridará diferentes datos, como la tasa de utilización del equipo asociado al conductor correspondiente, registro de los impactos, historial de carga de la batería, entre otros.
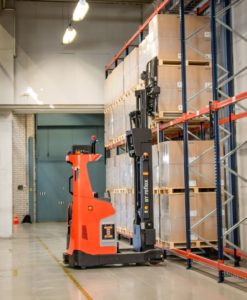
Ante estas características que presenta Toyota Material Handling en el mundo, la incógnita es que oportunidades existen en la Argentina para consolidar la tecnología de automatización en las operaciones logísticas locales. “A nivel de infraestructura, las instalaciones que hemos visitado están en perfecto estado. Algunos clientes están empezando a experimentar con estas soluciones y evaluando proyectos a futuro”, dijo Blom.
Måns Pontén aclaró que, si bien hay segmentos o tipos de productos más acordes a esta solución, la escalabilidad de rubros “es muy grande”. Sin dudas, esta tecnología tiene mucho para andar en el país. Las oportunidades están abiertas.
.
Nota publicada hoy en la sección Transporte & Logística de La Nación.